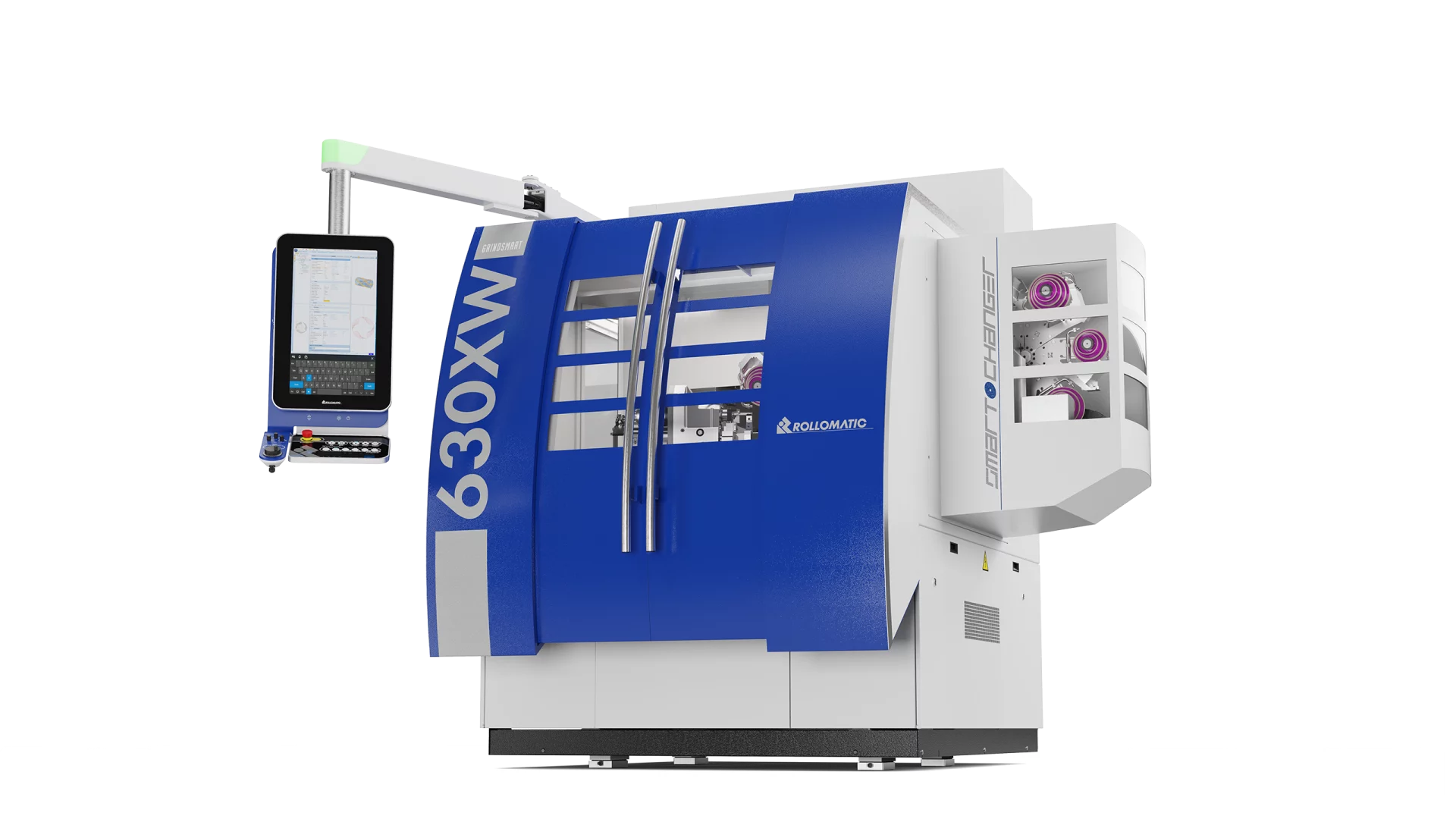
GrindSmart®630XW
Download the brochure
Please enter your email address to start downloading the brochure.
The 6-axis precision tool grinder GrindSmart®630XW has been designed for high performance and specialty tool manufacturing for both long and short batches.
It is equipped with linear motors, combined with the torque motor on the rotary axis, provides more benefits such as enhanced surface finish and reduced maintenance costs.
The oil used for cooling and lubricating the linear motors is the same as the coolant oil. This ensures consistent thermal stability during setup and production without incurring additional energy consumption.
The 6th axis concept of this machine is unique in the grinding industry. It provides improved accuracy on ballnose endmills, or corner radii with a possibility to incline the grinding wheels and allows for easier programming with shorter empty moves during grinding operations. This machine covers a wide range of diameters from Ø 0.1 to 20.0 mm (.004" - .75").
As standard, this model includes automatic high speed pick & place tool loader with a capacity of up to 1,360 tools along with a high-speed wheel & nozzle changer with 6 positions.
Smart Autonomous Grinding
Our goal is to satisfy our customers' demands and increase their competitiveness by constantly improving machining processes. Rollomatic's autonomous grinding concept and machine interface with third-party systems increases the level of production autonomy while maintaining geometric and dimensional tolerances.
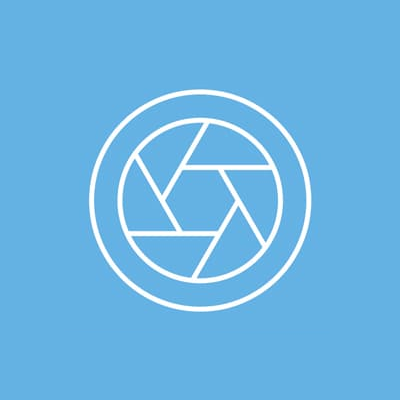
Smart Setup Assistant
The Smart Setup Assistant Function was developed with the aim of achieving the first ground tool within the tolerances.
The program generates a grinding path for each operation to be performed on the blank.
These grinding operations are carried out and then measured by the touch probe measuring system, whichdefines the grinding wheel corrections before the first tool is made.
The blank is then ground to the geometry programmed by the operator, taking into account the corrections required to ensure production according to specifications from the first tool.
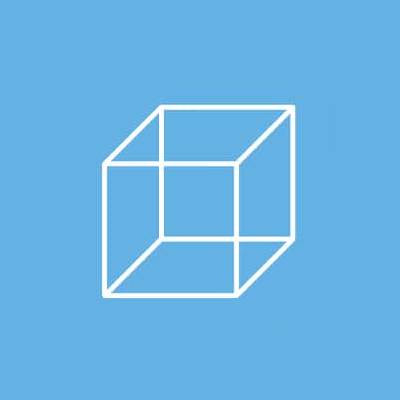
In-process Measurement
The in-process measurement function ensures that the tool remains within the defined tolerances throughout the production process.
To achieve this, several measurements are made periodically by the touch or laser measurement system to apply the necessary corrections, thus ensuring reliable and unattended production over an extended time.
Advantages
Patented shank guide and steady rest support to reach a concentricity of less than 0.002 mm
Short axis movements for greater stability and precision in production
Linear and torque motors provide mirror surface finish
Small footprint allows optimal use of available shop-floor space
JobManager software for unattended production of tools with different geometries
6-axis kinematics for more flexibility and precision
Enhanced productivity thanks to simultaneous changing of the wheel & nozzle packs during the tool loading/unloading cycle
High-performance synchronous spindle and redesigned HSK50 attachment provide consistent and high quality surface finish
Unique grinding capacity enables production of micro tools and large diameter tools all with the same machine
Smart features
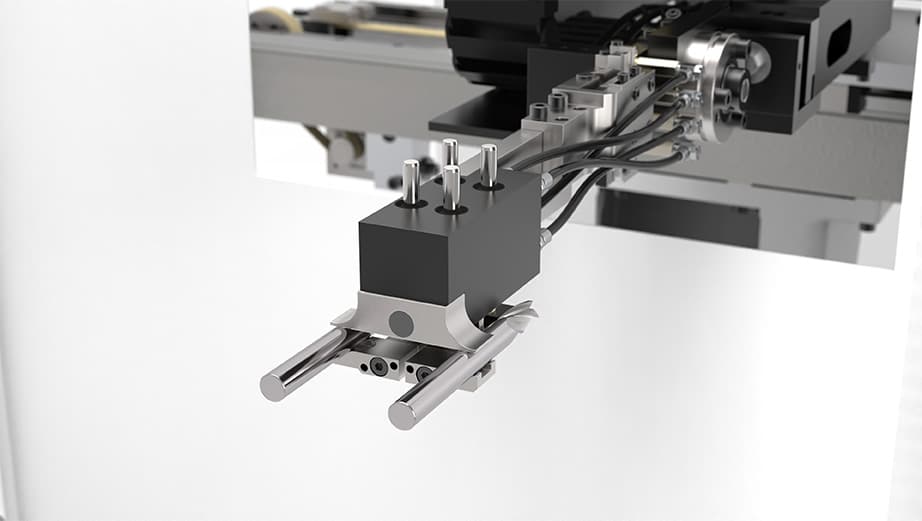
Smart Tool Loader
The high-speed tool loader, designed by Rollomatic and integrated into the basic machine, was developed with fast setup and ease-of-use in mind.
This is achieved by using pre-calibrated cassettes and clamps to hold different diameters without resetting the position.
Rollomatic automatic loaders are known to be the fastest and most reliable in our industry.
- Fast to set up
- Capacity up to 1’360 parts
- Robust, low maintenance design
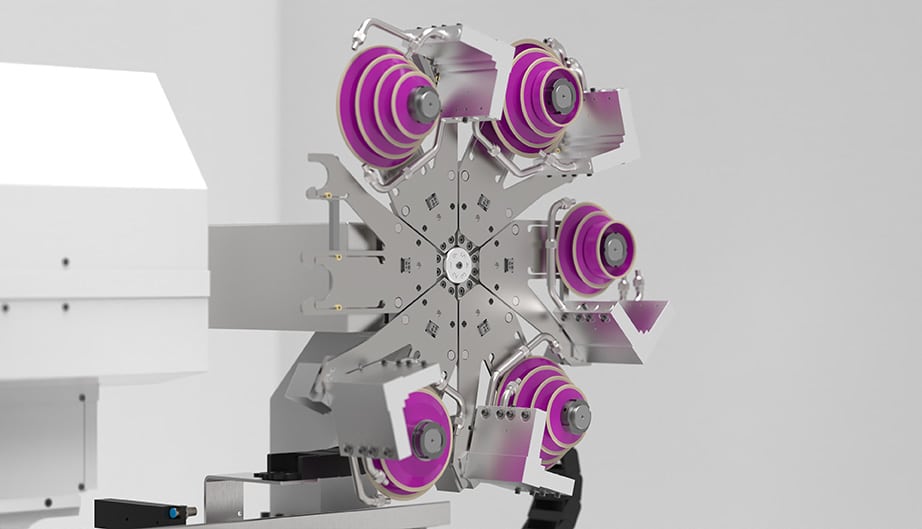
Smart Changer
Smart Changer is an ultra-fast automatic grinding wheel and nozzle changer that offers exceptional flexibility for the production of all types of tools.
The wheel changer can operate simultaneously with the tool loader, which substantially reduces cycle times.
- Increased flexibility
- 6-wheel pack capacity
- Ultra-precise wheel pack change, less than 0.002 mm
- Extended production autonomy
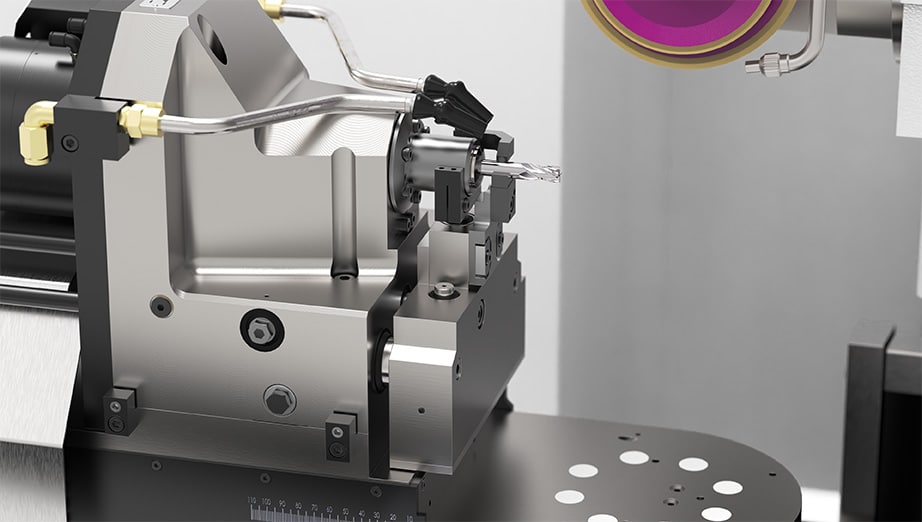
Smart Shank Guide
The Smart Shank Guide is a tool shank guiding system that guarantees concentricity down to a few microns at each clamping. It saves time and boosts productivity, as it is no longer necessary to probe for runout during setup.
- Exceptional concentricity accuracy, less than 0.002 mm at each clamping
- Quick and easy to set up
- Increased productivity
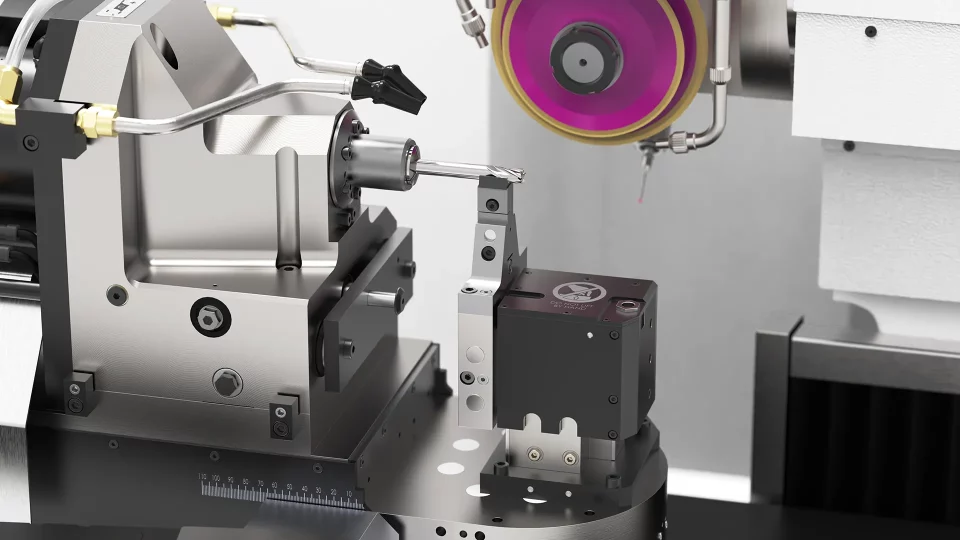
Smart Steady Rest
The Smart Steady Rest is a high precision steady rest for drills and other long tool blank. It provides stability in the grinding process and allows for faster feedrates.
This ensures repetitive quality of the tool throughout the production process.
- Quick and easy to set up
- Highly accurate adjustment system in 3 planes
- Consistent production quality
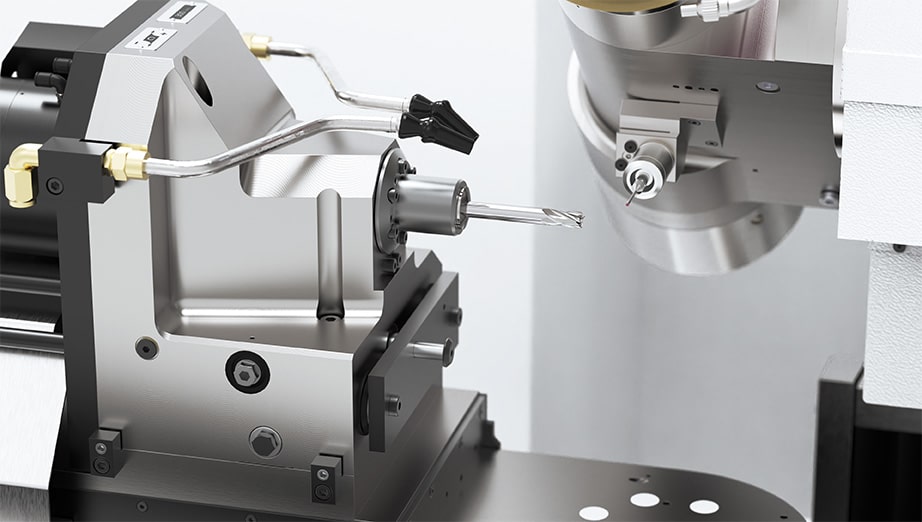
Smart Touch Probe
The Smart Touch Probe is a contact measurement system that allows the blank position to be defined before grinding and avoids variations during production. The system also compensates for machine thermal drift caused by changes in ambient temperature.- Runout compensation and core diameter measurement
- Setting assistance
- Superior stability during the production process
- Elimination of scrap during unattended production
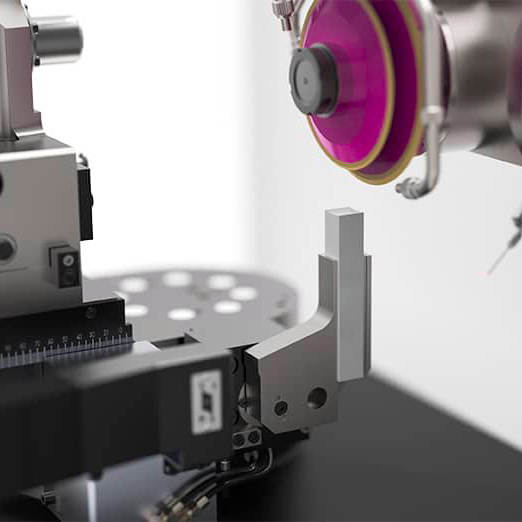
StickSmart®
The StickSmart® is an automatic sticking system for in-process cleaning of grinding wheels. The «stick», mounted in a holder, is used to regenerate superabrasive grinding wheels to maintain their cutting performance.
- Extends the working life of the wheel
- Extends unattended production cycles with high-performance wheels
- Reliable and safe automatic process for the operator
- Efficient, economical and safe solution
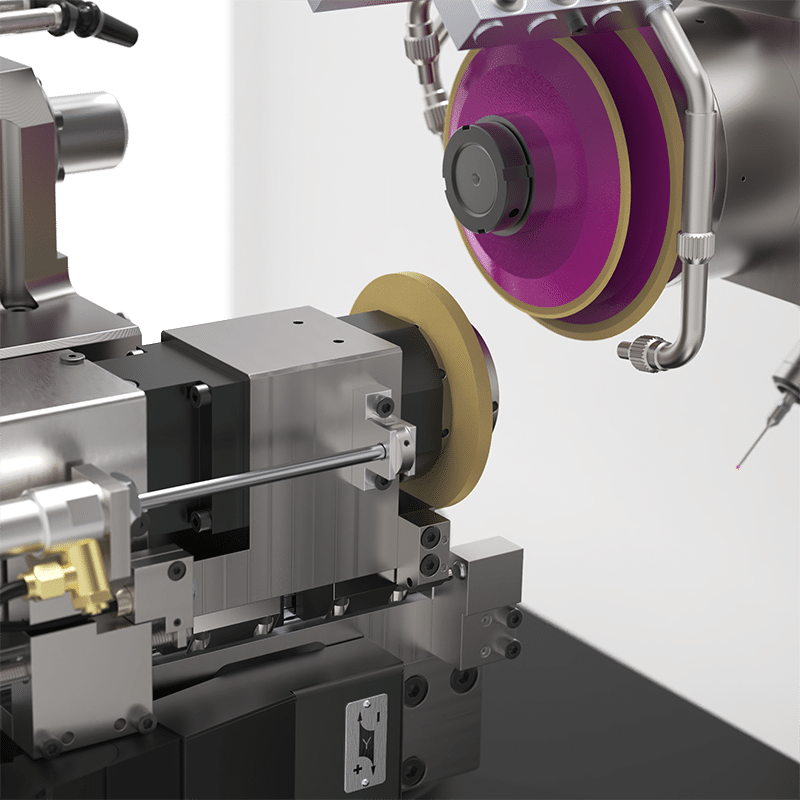
Smart in process Wheel Dresser
Smart in process Wheel Dresser is a self-retracting rotary dressing unit driven by a servo motor with a speed of up to 3,000 rpm.
This feature optimizes the service life of the grinding wheels. The maximum dressing wheel diameter is 125 mm for peripheral dressing of diamond and CBN wheels.
- Extended wheel life
- Optimization of production without interruption
- Constant maintenance of the wheel profile
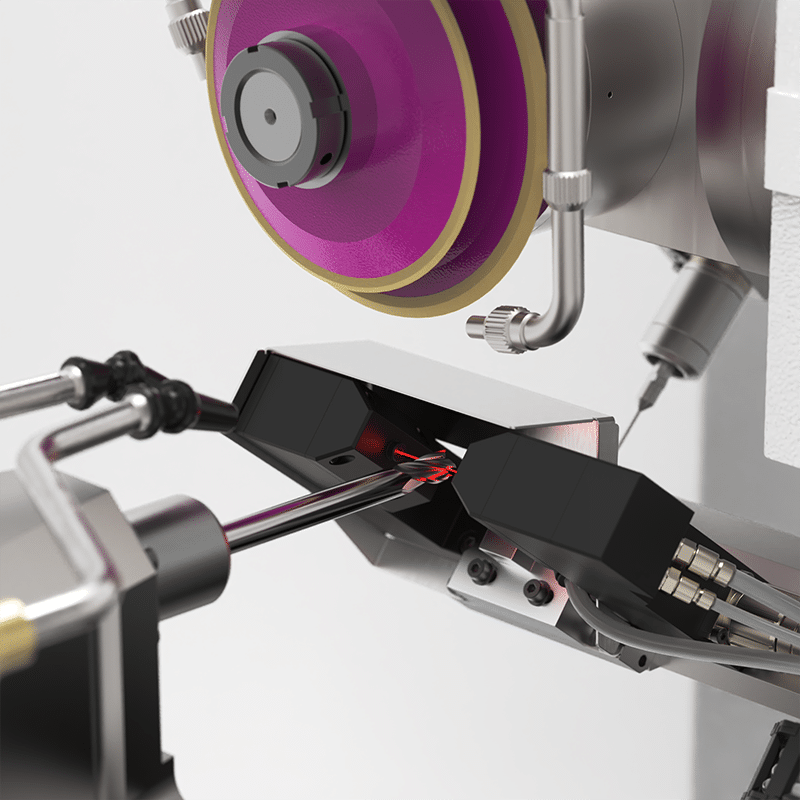
Smart Laser Measurement
The Smart Laser Measurement is a laser measurement unit for in-process inspection and automatic compensation.
This contactless tool measurement option enables reliable, unattended production within tight tolerances, increased productivity, elimination of scrap and cutting-edge damages.
- Wide range of measurable diameters from 0.3 mm to 20 mm
- No need for manual tool measurement during production
- Automatic compensation for tool diameter variations
- Superior stability during the production process
- Elimination of scrap during unattended production
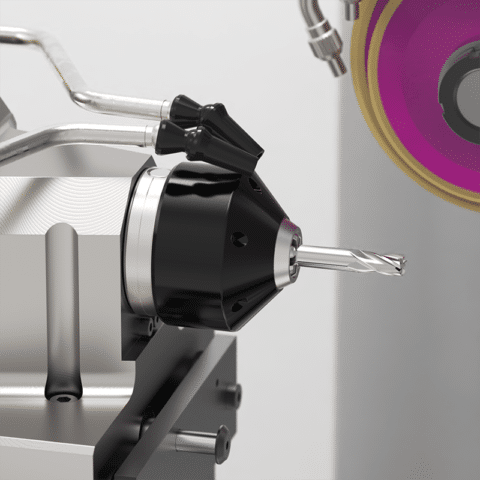
SmartChuck
The SmartChuck is a high-precision, self-centering multi-jaw clamping system that automatically adapts to different diameters without the need for adjustment. The SmartChuck can be used in conjunction with the automatic runout compensation feature included in the VirtualGrind®Pro programming software to ensure optimum concentricity. After a blank has been loaded in the clamping system it is measured with the probe. The measured values are then taken into account when tool paths are calculated, to ensure that the finished tool is produced within the concentricity tolerances of less than 0.005mm.- Clamping range from diameters of 3 to 12 mm
- Clamping concentricity less than 5 μm
- Easy-to-change production diameters, and quick and simple adjustment
Software
VirtualGrind®Pro
VirtualGrind®Pro is the innovative and powerful programming software that comes with Rollomatic GrindSmart® 5- and 6-axis CNC grinding machines.
VirtualGrind®Pro is intuitive, modern, user-friendly and flexible. A perfect combination with Rollomatic precision grinding machines, the user can program and grind all types of high-performance standard or special cutting tools.
Learn moreSmart Connectivity
Industry 4.0 is a constantly evolving world, and management tools have been developed to optimise its productivity. Rollomatic strives to develop connectivity solutions that are compliant with the UMATI standard, facilitating connections between peripherals in production processes and leveraging the available data
Learn moreFor Rollomatic, the process is as important as the machine. To better serve our customers, we are able to provide full turnkeys with every machine.
Turnkey
The turnkey process starts with our Sales Team and their help in defining your project.
Our expert team of Applications Engineers then studies your parts to determine the best machine, options, accessories, peripheral equipment, programs, and training required.
We can also offer Factory Acceptance and Site Acceptance Tests to ensure confidence in the machine and process.

Oil Filtration Systems

Mist Collectors

Balancing Machines

Wheel Presetting Machines

Programming

In Person & Virtual Training

Wheel Dressing & Truing Machines

Grinding Oils

Grinding Wheels

Metrology Equipment
We welcome the opportunity to be a part of your success!